Protótipo de quarto de hotel modular mostra aos investidores globais a velocidade e a versatilidade da construção modular
A Forta PRO, fabricante de construções modulares da Letônia, fez recentemente uma parceria com a Marriott para criar um quarto de hotel modular com base em seu projeto atual, o Moxy. Os dois se conectaram em Copenhague em 2019, quando a Marriott manifestou interesse em criar uma maquete para mostrar aos investidores a qualidade disponível por meio de técnicas de construção modular. O quarto autônomo está atualmente localizado em Frankfurt e está disponível para os investidores visitarem.
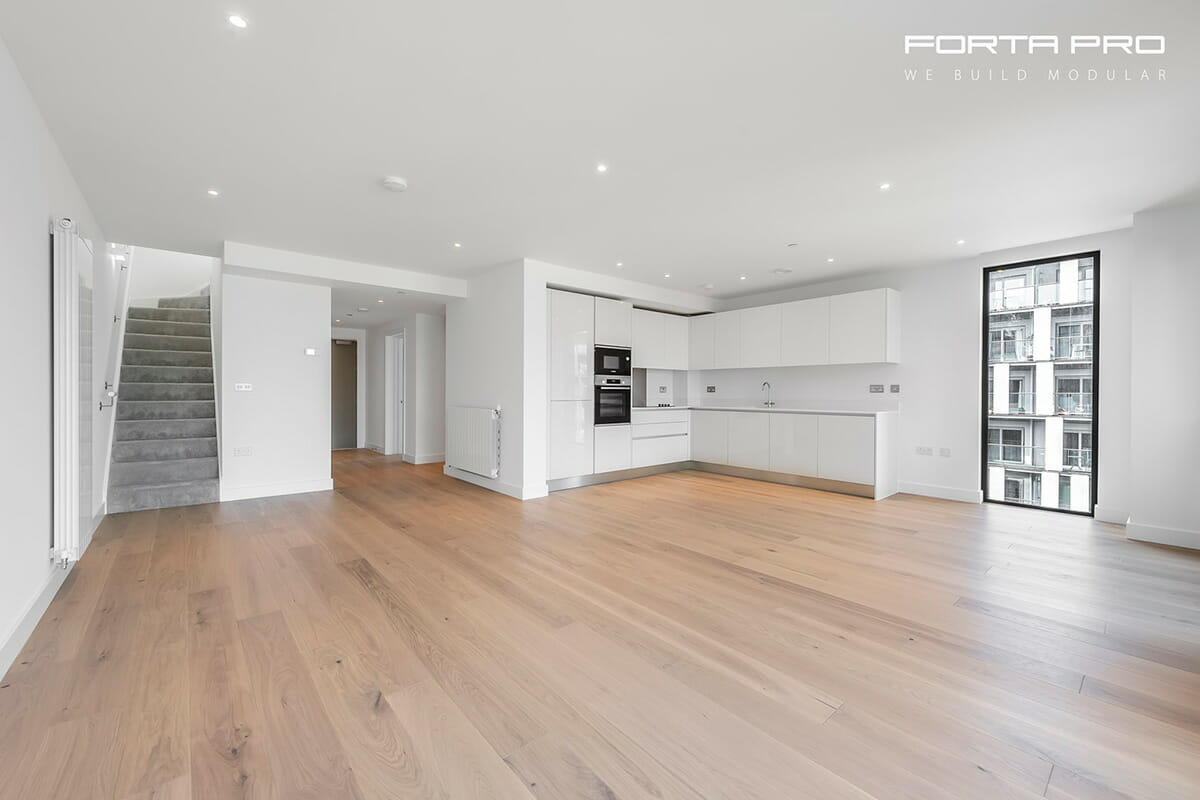
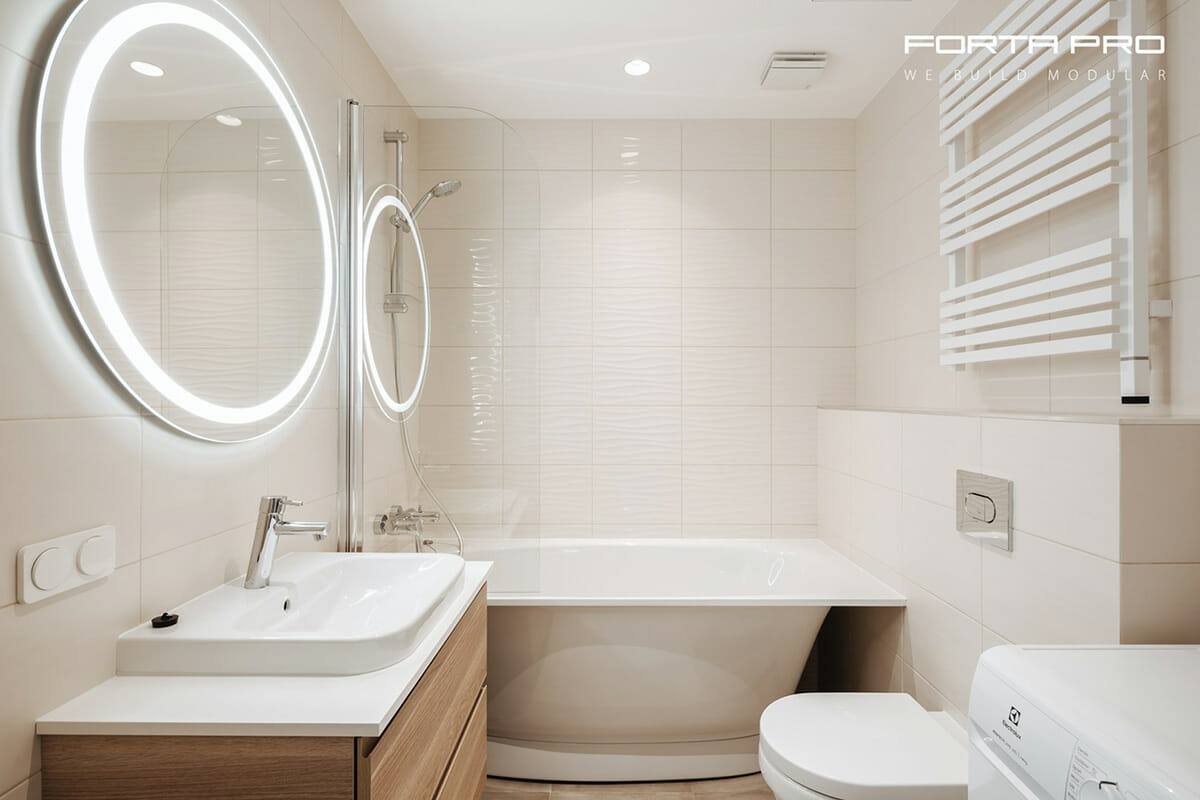
Kristaps Miķelsons, Diretor de Tecnologia da Forta PRO, explicou que o projeto foi relativamente simples, pois o Marriott Moxy tinha um livro de projeto para cada tipo de quarto que listava as especificações de materiais, dimensões e outras informações. A Forta PRO traduziu esses projetos em desenhos modulares, eles foram aprovados pela Marriott e, em seguida, a Forta PRO encomendou os materiais de acabamento dos fornecedores da Marriott.
De acordo com Miķelsons, o objetivo do protótipo era "dissipar as dúvidas das pessoas e mostrar as possibilidades da construção modular". A Marriott queria mostrar aos investidores a qualidade aprimorada e a maior velocidade disponíveis por meio de um processo modular. A esperança era que os investidores ficassem impressionados e fizessem parceria com a Marriott em desenvolvimentos futuros.
O projeto teve seus desafios. Como a empresa está acostumada a produzir módulos que são colocados dentro de um edifício, o protótipo teve de ser especialmente construído com um exterior capaz de resistir aos elementos. Além disso, houve atrasos no envio de materiais, bem como a dificuldade de entregar o módulo em seu local de descanso final quando um guindaste não podia ser instalado no local devido a uma estrutura de estacionamento subterrâneo. O guindaste teve que ser estacionado em um posto de gasolina próximo e os movimentos tiveram que ser feitos com precisão cirúrgica.
Apesar dessas dificuldades, o projeto parece ter sido um sucesso, já que os dois estão atualmente trabalhando juntos em vários projetos potenciais.
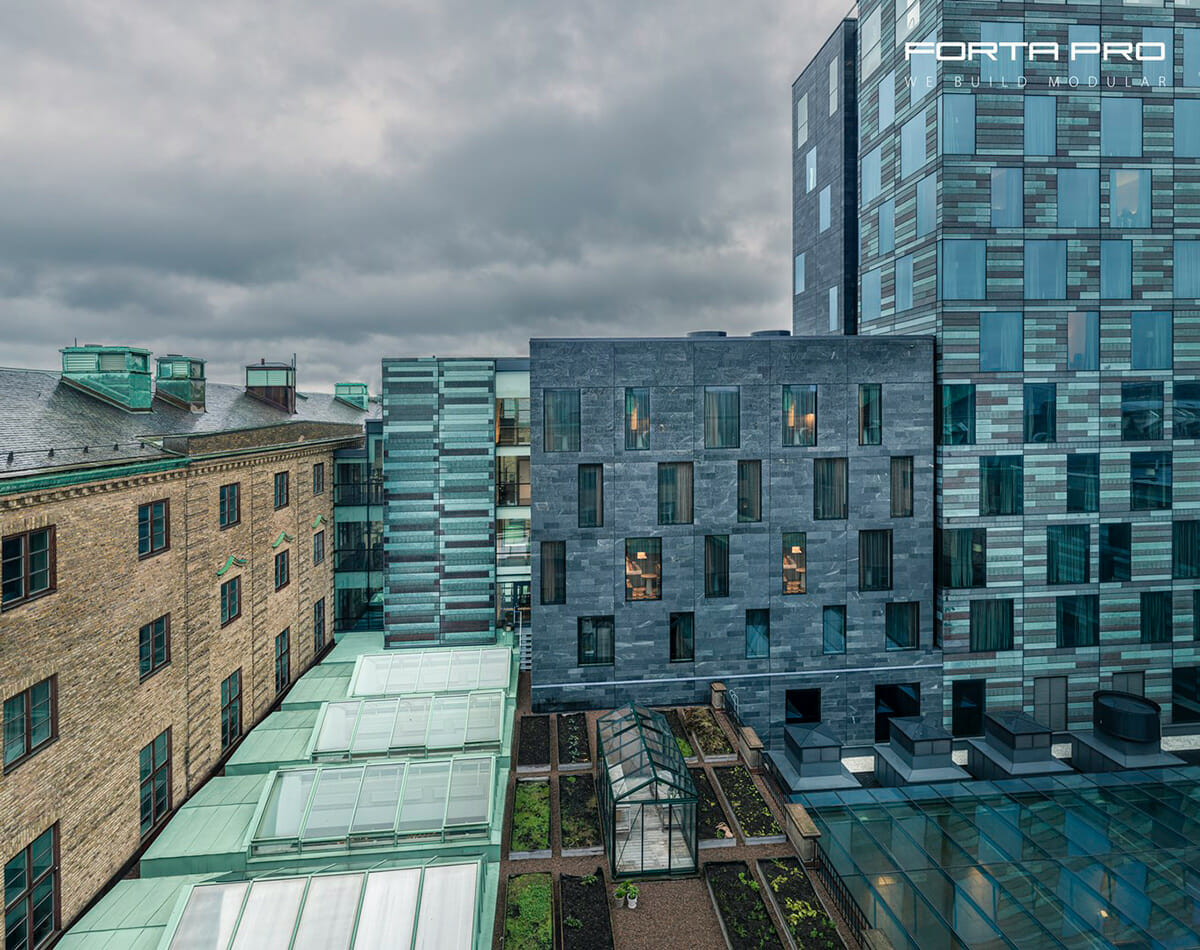
Desde então até agora
A Forta PRO começou em novembro de 2013 como SIA Forta Medical, pois a empresa estava produzindo soluções modulares de alta qualidade para instalações e equipamentos médicos. Em março de 2018, o nome foi alterado para SIA Forta Prefab e a marca Forta PRO começou.
Atualmente, a empresa é especializada em edifícios modulares multifamiliares e comerciais de vários andares, incluindo edifícios médicos, hotéis, apartamentos, dormitórios e PODs de banheiro. A empresa tem duas fábricas, sendo a principal em Ventspils, na Letônia, e a outra em Jelgava, na Letônia, e a produção total é de 120.000 metros quadrados por ano. A fábrica de Ventspils opera quatro linhas de produção com capacidade de até quatro módulos por dia e 75.000 metros quadrados por ano. Cada módulo leva cerca de vinte dias para ser construído. Seus projetos estão localizados principalmente nos países escandinavos, no Reino Unido, na Alemanha e em outros países do norte da Europa.
Aprimoramentos no design e na produção
A vantagem de seu projeto para edifícios modulares de vários andares é a resistência estrutural proporcionada por uma estrutura rígida de aço. Com essa estrutura, eles podem construir edifícios de até oito andares de altura sem reforço adicional. Os edifícios com mais de oito andares exigem um núcleo de concreto.
Os módulos são aparafusados uns aos outros e à laje da fundação. Placas de gesso e estruturas de aço leve são usadas nas paredes internas, e lã mineral é fornecida para isolamento. Seu processo de produção conta com pelo menos vinte verificações de qualidade para garantir a qualidade e a resistência de cada módulo.
Os shafts para redes mecânicas, elétricas e de encanamento estão incluídos nos módulos e serão conectados a esses sistemas no local. Os corredores comuns são deixados sem acabamento para facilitar as conexões de utilidades. Com essa configuração, muitas das conexões dos módulos podem ser concluídas sem entrar nas salas dos módulos.
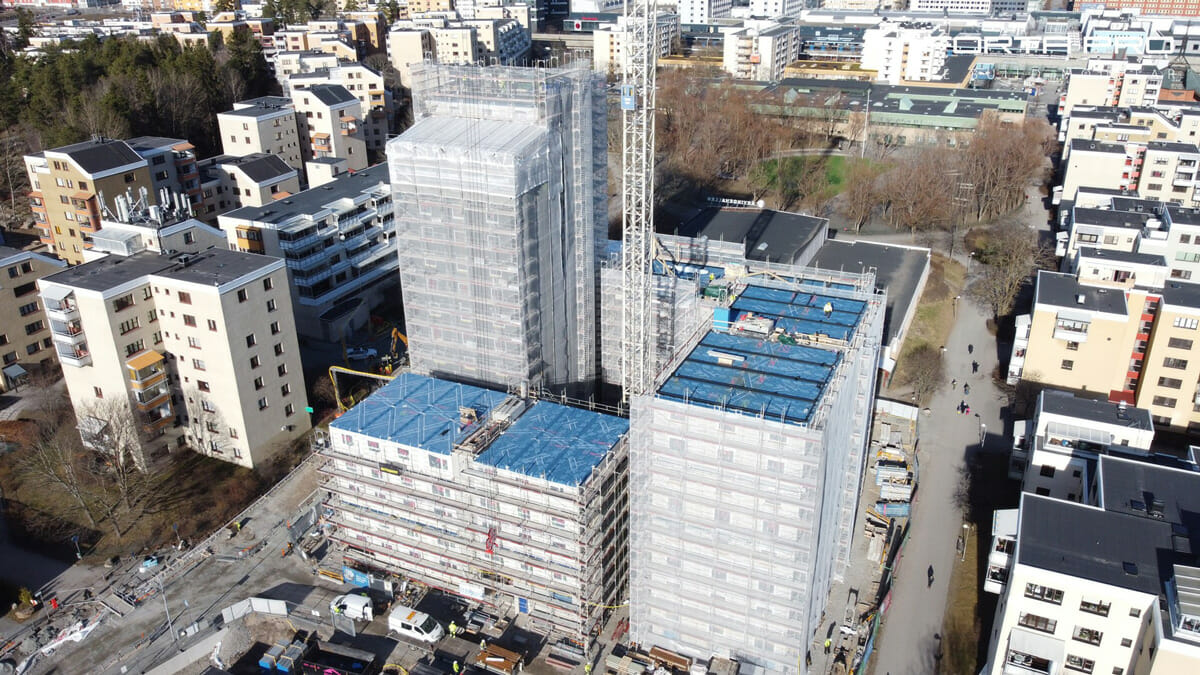
Os benefícios da construção modular
Ao falar sobre o processo de construção modular, Aviv Brosilovski, responsável pelo desenvolvimento de negócios, enfatiza três vantagens principais em relação à construção tradicional, incluindo cronogramas de projeto reduzidos, controle de qualidade e economia de custos.
Os cronogramas dos projetos são mais curtos devido à velocidade obtida com o design repetitivo, que geralmente é encontrado em projetos de residências multifamiliares e hotéis. Como muitas das unidades são projetadas de forma semelhante e se repetem várias vezes ao longo do projeto, o design pode ser facilmente replicado com o uso de módulos. Além disso, a velocidade é maior porque o trabalho nos módulos está em andamento enquanto o trabalho no local está sendo concluído. Essa capacidade de programar o trabalho simultaneamente pode economizar um tempo significativo no cronograma do projeto.
Como a construção modular ocorre em ambientes de fábrica controlados, a qualidade pode ser rigorosamente monitorada e controlada. Os processos de produção podem ser padronizados e o maquinário preciso, como robôs e impressoras 3D, pode ajudar a garantir a qualidade das unidades de construção, o que é particularmente importante para projetos maiores.
As fontes de economia de custos incluem redução dos custos de mão de obra devido à eficiência, minimização do desperdício de material e geração antecipada de receita devido à conclusão mais rápida do projeto. Essas economias geralmente compensam o custo inicial de investimento em métodos de construção modular.
A Forta PRO teve que fazer algumas alterações em sua cadeia de suprimentos devido ao conflito na Ucrânia. Eles observaram um aumento nos custos de energia e atrasos de materiais que afetaram a programação do projeto. Com o fornecimento de materiais de outros locais, eles conseguiram continuar a ser produtivos. Como muitos outros, eles esperam uma solução rápida e um retorno ao relacionamento com seus parceiros ucranianos com os quais trabalharam ao longo dos anos.
Um futuro brilhante
Por esses motivos e muitos outros, a Forta PRO espera que o mercado de construção modular continue a crescer. Brosilovski acredita que técnicas de fabricação aprimoradas e automatizadas continuarão a melhorar a precisão, a qualidade e a escalabilidade da construção modular. Para ele, avanços como robótica, impressão 3D e automação levarão a projetos mais complexos e inovadores. Ele também considera a sustentabilidade um fator importante, pois mais empresas estão procurando incorporar recursos de eficiência energética, energia renovável e materiais ecologicamente corretos, o que ajudará a impulsionar a tendência contínua de práticas de construção mais ecológicas e regulamentações ambientais mais rígidas. A versatilidade dos projetos modulares é outra maneira pela qual o mercado pode crescer. Os desenvolvimentos nas áreas de saúde, educação, hotelaria e infraestrutura podem ser os projetos modulares do futuro.
O futuro da Forta PRO continua a levá-la a novos mercados. A empresa uniu forças com a Samsung C&T da Coreia do Sul para desenvolver planos de expansão na Letônia e em outros países. O objetivo é expandir o uso da construção modular e abrir e operar fábricas modulares em todo o mundo. Eles também planejam compartilhar o conhecimento que adquiriram com anos de experiência em construção modular. As duas empresas já têm um histórico de trabalho conjunto em muitos projetos, portanto a parceria é uma extensão desse relacionamento.
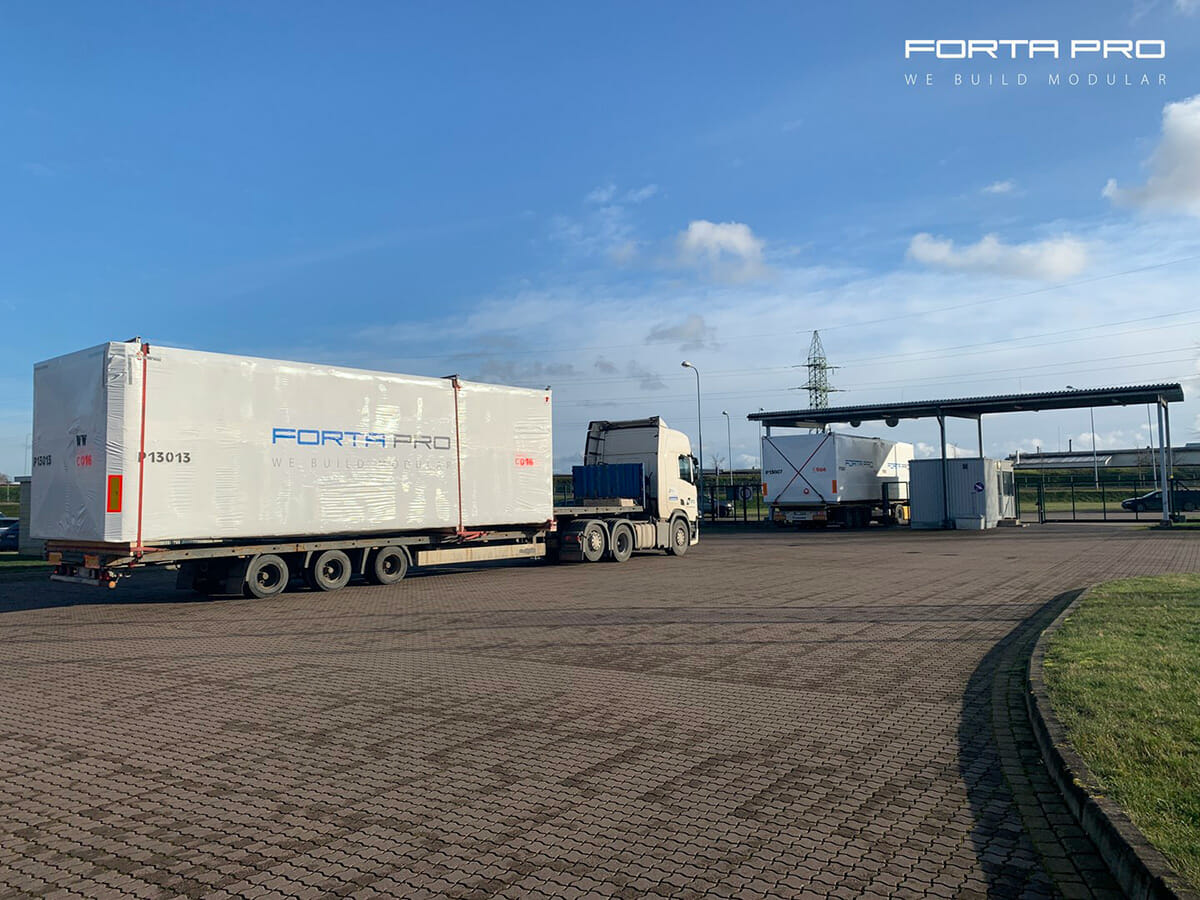
A empresa foi homenageada com duas indicações como finalista do Projeto Internacional do Ano no concurso Offsite Awards 2023. Os projetos indicados são o Hage's Badehotel e o Unity Malmö. O Badehotel é um hotel construído com unidades modulares na Dinamarca, enquanto o Unity Malmö é um grande empreendimento de apartamentos modulares na Suécia. A Forta PRO já foi reconhecida anteriormente com prêmios semelhantes. Em 2020, o projeto Berkeley Homes, um prédio de apartamentos em Londres, ganhou o prêmio Private Housing Project of the Year. Em 2021, o Project Jylland, um projeto de moradia estudantil na Suécia, ganhou o prêmio International Offsite Project of the Year. Os vencedores deste ano serão anunciados na Offsite Expo em Coventry, Reino Unido, em 19 de setembro de 2023.
Sobre o autor: Dawn Killough é escritora freelancer de construção com mais de 25 anos de experiência trabalhando com empresas de construção, subcontratadas e empreiteiras gerais. Seus trabalhos publicados podem ser encontrados em dkilloughwriter.com.
Mais sobre a Modular Advantage
Como a BIM e a IA estão melhorando os resultados da construção modular em toda a Europa
A digitalização e o software de modelagem de projetos em constante evolução têm ajudado os fabricantes, construtores e projetistas tradicionais há anos. Mais recentemente, as partes interessadas em construção modular e externa com experiência em tecnologia também adotaram essas ferramentas, adicionando seus próprios conhecimentos e dados para criar maneiras mais novas, mais rápidas e mais eficientes de construir. Juntamente com as novas ferramentas baseadas em BIM e IA, esses construtores estão agora ampliando os limites do que é possível com a construção fora do local e o gerenciamento de energia.
Proposta de salário prevalecente do Oregon: Um alerta para a construção modular
Se o Projeto de Lei 2688A se tornar lei, os projetos de construção aumentarão de preço, enfrentarão prazos de conclusão mais longos e produzirão muito mais resíduos. O projeto de lei também incentiva a concessão de contratos a empresas de fora do estado que não reinvestiriam seus ganhos na economia local do Oregon.
Por trás do design do Bethany Senior Terraces, o primeiro projeto modular de moradia para idosos Passive House de Nova York
À medida que mais desenvolvedores buscam atender às novas regulamentações de eficiência energética, a equipe da Murray Engineering estabeleceu um novo recorde. Com o projeto Bethany Senior Terraces, a Murray Engineering ajudou a desenvolver a primeira estrutura modular de Nova York que engloba totalmente os princípios da casa passiva, introduzindo uma nova era de eficiência energética na cidade que nunca dorme.
Como a LAMOD está usando o modular para lidar com a ineficiência, a sustentabilidade e o futuro da construção
À medida que desenvolvedores, projetistas e empreiteiros procuram entender as necessidades em evolução do setor modular, ninguém é tão versado nos benefícios da modularização quanto Mārcis Kreičmanis. Como cofundador e CBDO da LAMOD em Riga, na Letônia, Mārcis estabeleceu como seu objetivo final abordar as ineficiências da construção tradicional.
De construtor de móveis a 'arquiteto ativista': A jornada única de Stuart Emmons
Stuart Emmons era fascinado por construções desde muito jovem. Ele se lembra de construir cidades de areia com seu irmão durante viagens à costa de Jersey. Seu pai lhe deu sua primeira mesa de desenho aos dez anos de idade. Hoje, ele é um arquiteto experiente que recebeu seu FAIA em junho de 2025. O caminho que ele percorreu é único, para dizer o mínimo.
Forge Craft Architecture + Design: Códigos, contratos e propriedade intelectual
O diretor fundador e diretor de prática modular da Forge Craft Architecture + Design, Rommel Sulit, discute as implicações de códigos, contratos e propriedade intelectual na
construção modular.
Eisa Lee, a arquiteta "bilíngue
Agora, como fundadora da XL
Architecture and Modular Design em Ontário, Canadá, ela aplica não apenas sua formação como arquiteta tradicional, mas também uma visão holística completa do design modular. É essa visão abrangente que orienta seu trabalho para ser uma verdadeira parceira que preenche a lacuna entre arquitetos e fábricas modulares à medida que colaboram no processo de design.
Tamarack Grove Engineering: Projetando para o setor modular
A função de um engenheiro estrutural é crucial para o sucesso de um projeto modular, desde a análise inicial até a administração da construção. A Tamarack Grove oferece serviços de engenharia estrutural - análise de projetos, criação de planos, criação de projetos e administração da construção - para áreas comerciais, de manufatura, instalações, serviços públicos e modulares. O setor modular é apenas um dos setores de mercado que a empresa atende, mas é um setor cada vez mais popular.
Engenheiro domina a arte de ouvir seus clientes
Desde que fundou a Modular Structural Consultants, LLC. em 2014, Yurianto estabeleceu um número constante de clientes de construção modular e baseada em contêineres, principalmente fabricantes. Seus serviços geralmente incluem o fornecimento de cálculos de engenharia, revisão de desenhos e certificação de engenharia
Por dentro da College Road: Engineering the Modules of One of the Tallest Modular Buildings (Engenharia dos módulos de um dos edifícios modulares mais altos do mundo)
College Road é um empreendimento residencial modular inovador em East Croydon, no sul de Londres, desenvolvido pela incorporadora e empreiteira Tide, sua empresa modular Vision Volumetric (VV), e projetado pela MJH Structural Engineers.